SPACESHIP 60 BUILD: Infusion, what put us on the map
- Nic de Mey
- Apr 4, 2023
- 3 min read
Updated: Oct 5, 2023
Above all, when involved in the construction of large, state-of-the-art composite yachts, the significance of having a highly skilled workforce cannot be emphasized enough. When your employees are regularly exposed to resin and fumes, attracting and retaining top-tier personnel can pose a considerable challenge. However, infusion offers an exceedingly clean and effective alternative. In this method, all the layers and core materials are initially placed in a dry state. Subsequently, a vacuum bag is applied, and resin is introduced through tubes via a flow medium into the laminate. This results in a uniform distribution of resin throughout the entire component, maintaining a resin-to-fiber ratio of approximately 40% resin to 60% fiber. To put it in practical terms, if a part, excluding the core, weighs 10 kilograms, 6 kilograms would consist of fiber, while 4 kilograms would be resin.
Embracing infusion allows our staff to come to work each day, produce components day in and day out, and maintain a clean and tidy workspace. This process enables them to produce accurate work and take pride in their workplace consistently and whilst you can argue that the consumables such as tubes, taps and bag plastic are an added expense to a project I firmly believe that the savings in a clean shop and high caliber staff turning up every day more than offsets this cost
Furthermore, one of the substantial advantages of resin infusion lies in its ability to create an exceptional bond with the core material. This bond is arguably the single most crucial aspect when constructing advanced composite vessels. We have a strong suspicion that infusion significantly mitigates issues related to core out-gassing, which is a complex topic on its own but can pose severe challenges for boatyards if it occurs. With infusion, the resulting bond to the core is so robust and devoid of voids that separating a composite skin from the core is virtually impossible without resorting to grinding, I simply don't believe that traditional lay-up and core bonding techniques come close to an infused part.
From the customer's point of view, they are well aware that they are receiving a boat crafted to be as lightweight as possible while maintaining exceptional strength. We are acutely conscious of environmental concerns, recognizing that constructing a boat burdened with unnecessary weight is counterproductive. Essentially, this would entail expending energy to propel the boat through the water throughout its potentially lengthy lifespan, which could extend to a century or more.
We transitioned into becoming an infusion-focused facility during the initial phases of its adoption here in New Zealand. The journey to achieving proficiency in infusing large components has been a gradual one. The potential consequences of failure in the absence of proper procedures are indeed daunting. To mitigate these risks, we have implemented stringent quality control protocols that serve as a safeguard against any mishaps. The outcome of our unwavering discipline in this regard is our ability to consistently produce intricate and precise components day after day.
Our 2 current SpaceShip 60 builds represents the epitome of the resin infusion method. Every single part and connection undergoes the infusion process, with comprehensive quality control sheets meticulously filled out for each component, regardless of its size. These records are diligently maintained to guarantee that every element is constructed in precise accordance with specifications. Remarkably, failures during the manufacturing of these parts are exceedingly rare due to our rigorous adherence to these processes.
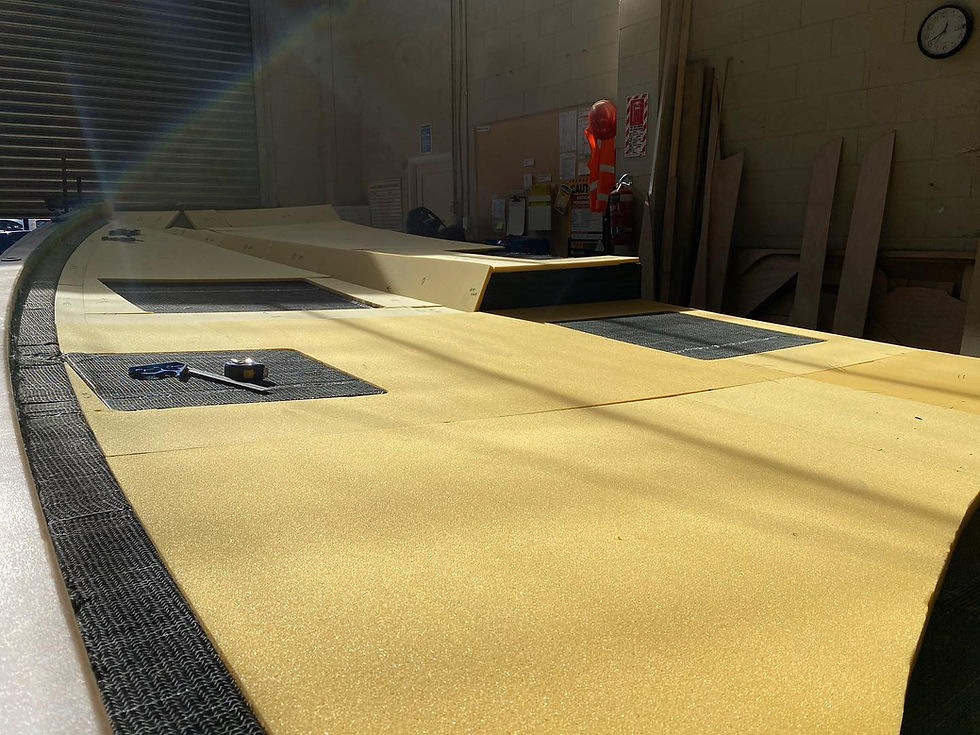





Comments